Tuy nhiên, với mức độ tự động hóa ngày càng cao, hoạt động bảo dưỡng phòng ngừa đòi hỏi nhiều nhân lực chuyên môn cho bộ phận bảo dưỡng, thậm chí có khi còn cao hơn số lượng người vận hành. Điều này khiến các nhà quản lý phải tìm cách thay đổi, theo đó người vận hành phải đảm nhiệm cả công việc bảo dưỡng hàng ngày còn bộ phận bảo dưỡng chuyên trách sẽ quản lý và đảm nhiệm các công tác bảo dưỡng quan trọng định kỳ. Khái niệm bảo dưỡng tự quản (Autonomous Maintenance - AM), một trong 8 trụ cột quan trọng của TPM cũng được xuất hiện từ đây.
Các trụ cột chính của TPM
TPM với 8 trụ cột chính với nền tảng là hoạt động 5S, khởi đầu cho việc phát hiện các vấn đề để tiến hành các hoạt động cải tiến trong TPM. Trong đó ý nghĩa của từng trụ cột như sau:
Autonomus Maintenance: Bảo trì tự quản, mục đích người vận hành máy biết sửa chữa, bảo trì máy và nhận diện các hư hỏng ở một mức độ nhất định. Công việc này giúp người vận hành biết về kết cấu và chức năng của máy, hiểu về quan hệ giữa máy móc và chất lượng, quen với việc tuân thủ nghiêm ngặt các quy định từ đó phát hiện và chẩn đoán chính xác mọi bất thường của máy cũng như cách khắc phục nhanh chóng và phù hợp.
Planned Maitenance: Bảo trì có kế hoạch, nhằm thực hiện phương châm “phòng bệnh hơn chữa bệnh” để tránh dừng máy, tránh các lỗi lặp lại, tăng tuổi thọ máy, giảm thời gian sửa chữa và chi phí cho công tác bảo trì. Đồng thời có kế hoạch sử dụng thích hợp cho những máy móc thiết bị mới ngay từ khi bắt đầu đưa vào hoạt động.
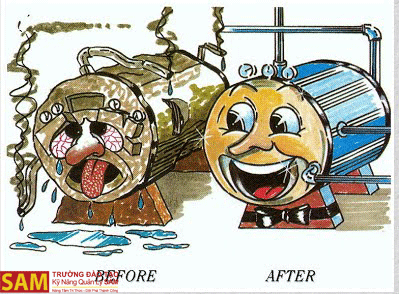
Focus Improvement: Cải tiến có trọng điểm, thực tế tại mỗi tổ chức luôn phát sinh những vấn đề, như: chất lượng, chi phí, năng suất, an toàn lao động ... tuỳ theo từng thời điểm, ý nghĩa và mức độ cần thiết của sự việc trong thời điểm đó, người ta sẽ chọn lựa đưa ra vấn đề và thành lập một nhóm hay một số nhóm để tập trung cải tiến các vấn đề đó. Bên cạnh đó vẫn khuyến khích những sáng kiến cải tiến nhỏ của từng cá nhân hoặc từng bộ phận trong tổ chức. Tất cả hoạt động trên đều nằm trong chiến lược phát triển của tổ chức là cải tiến liên tục. Nhưng ở đây muốn nhấn mạnh một điều nếu tập trung tất cả nguồn lực vào một, hay một số mục tiêu lựa chọn trước thì dễ dẫn đến thành công mà không lãng phí thời gian, công sức.
Quality Maintenance: Bảo trì chất lượng, nhằm xây dựng, duy trì và quản lý một hệ thống quản lý chất lượng tốt, kiểm soát chất lượng từ khâu đầu tiên đến khâu phân phối và hậu mãi, có hệ thống khắc phục và phòng ngừa. Đồng thời phân tích quá trình sản xuất để tìm ra các điểm dễ xảy ra lỗi và tiến hành khắc phục thích hợp.
Initiative Management: Quản lý cải tiến, nhằm quản lý và học hỏi từ những cải tiến trước đó, tất cả người vận hành đều tham gia vào việc đề xuất các ý tưởng cải tiến cho công việc liên quan đến quá trình, thiết bị máy móc của mình.
Education & Training: Đào tạo, nếu không có quá trình đào tạo thích hợp và chuẩn hóa, TPM và hệ thống bảo trì nói chung, sẽ không thành hiện thực. Việc đào tạo phải đảm bảo chất lượng, hiệu quả.
Safety, Health and Environment (SHE): An toàn, sức khỏe và môi trường, hướng tới không có tai nạn lao động, không có bệnh nghề nghiệp, không tác động xấu đến môi trường. Đặc biệt nhấn mạnh đến an toàn, sức khỏe và môi trường làm việc của người vận hành thiết bị.
Office TPM: Hoạt động TPM các phòng ban gián tiếp hỗ trợ cho bộ phận sản xuất … nhiệm vụ của họ là thu thập, xử lý, cung cấp thông tin, phục vụ các nhu cầu khác của sản xuất.
Với sự giải thích các trụ cột chính của TPM ở trên có thể dễ dàng hiểu được ý nghĩa và vai trò của hoạt động TPM trong việc nâng cao hiệu suất sử dụng của thiết bị máy móc với sự tham gia của tất cả các thành viên trong tổ chức. Tuy nhiên điều khó khăn duy nhất là làm sao có thể triển khai thực hiện được những ý nghĩa và mong muốn đó thành các hành động thực tế và cụ thể đã là một điều khó. Và khi áp dụng các triết lý đó của TPM vào các ngành công nghiệp khác nhau với các đặc thù khác nhau thì lại càng khó khăn gấp bội, và không phải doanh nghiệp nào ở trên thế giới hay Việt Nam cũng có thể triển khai thành công.
Mục tiêu cơ bản của TPM:
Trong TPM, một chỉ số đánh giá hiệu quả của thiết bị đó là “Hiệu suất thiết bị toàn phần” OEE - Overall Equipment Effectiveness.
Công thức tính chỉ số được tính theo công thức sau: OEE = A x P x Q
Trong đó:
A - Mức độ sẵn sàng của thiết bị
A = (Thời gian máy chạy thực tế/ Thời gian chạy máy theo kế hoạch) x 100%
P - Hiệu suất thiết bị
P = (Công suất thực tế/ Công suất thiết kế) x 100%
Q – Mức chất lượng sản phẩm
Q = (Số lượng sản phẩm đạt chất lượng/ Số lượng sản phẩm sản xuất ra) x 100%
Các nghiên cứu trên thế giới chỉ ra rằng OEE trung bình của các nhà máy sản xuất khoảng 60%. Đối với các nhà máy được quản lý tốt theo chuẩn thế giới phải có OEE khoảng 85 % trở lên, với các yếu tố cấu thành như sau:
- Availability A: 90 %
- Performance P: 95 %
- Quality Q: 99.99 %
Theo cách tính trên thì với thực tế hiện nay tại doanh nghiệp sản xuất, cụ thể tại NBC với 1 ca sản xuất 8 tiếng, chưa tính đến thời gian nghỉ ca, thời gian dừng máy ngắn để thiết lập thông số, hay thời gian máy hỏng phải dừng để sửa chữa, thì mức độ sẵn sàng của thiết bị mới chỉ đạt
A = (8/24) x 100% = 33%.
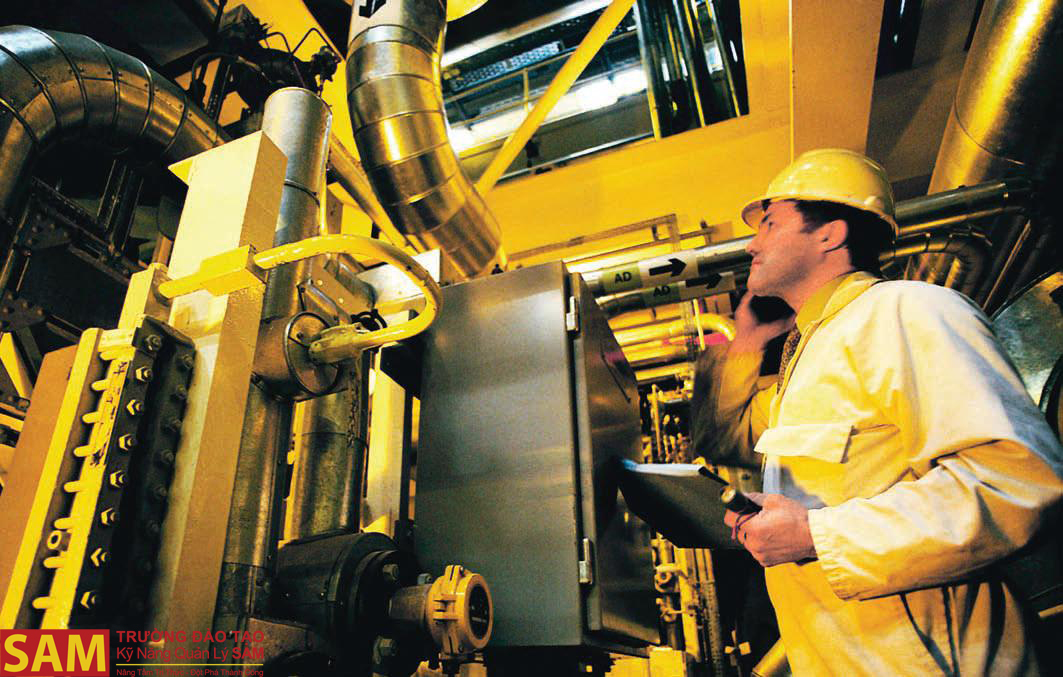
Hiệu suất thiết bị P đạt theo công suất thiết kế khoảng 70% vì nhiều lý do như tay nghề công nhân chưa được đảm bảo, còn nhiều lãng phí trong thao tác, quy trình vận hành, thậm chí là không dám chạy ở tốc độ/công suất thiết kế của thiết bị vì không “dám chắc” thiết bị chạy ổn định được trong thời gian dài và liên tục ở tốc độ như vậy không.
Mức chất lượng sản phẩm Q đạt tỷ lệ khoảng 80%
Như vậy thì thực tế tại NBC, chỉ số: OEE = A x P x Q = 33% x 70% x 80% = 18.5%
Đó chính là điểm mấu chốt khi xem xét quyết định về việc đầu tư thiết bị công nghệ và mở rộng sản xuất hay tăng năng lực sản xuất của doanh nghiệp
Hướng dẫn sử dụng thẻ treo theo mô hình TPM
“Hoạt động Thẻ treo” dựa trên nền tảng của hoạt động 5S nhằm phát hiện các khiếm khuyết của thiết bị máy móc cũng như là môi trường làm việc, văn phòng nhà xưởng. Theo nội dung của chương trình thì đây là một hành động cần thiết nhằm:
- Ngăn chặn sự xuống cấp của thiết bị
- Từng bước đưa thiết bị về tình trạng ban đầu
- Duy trì thiết bị ở điều kiện làm việc ổn định, tin cậy
- Đảm bảo sự sẵn sàng làm việc của thiết bị khi cần thiết.
Thẻ treo khiếm khuyết với 7 loại khiếm khuyết cơ bản
Dưới quan điểm của các chuyên gia tư vấn cùng với sự mong mỏi nâng cao hiệu quả đầu tư thiết bị công nghệ thì cần phải nâng cao để chỉ số OEE lên cao hơn nữa. Hoạt động thẻ treo với mục tiêu đưa tình trạng thiết bị về trạng thái ban đầu để phục vụ sản xuất mới chỉ là bước cần thiết đầu tiên. Sau khi đạt được bước đầu tiên này, đó sẽ là điều kiện nền tảng để thiết bị có thể tham gia sản xuất liên tục từ 8 tiếng đến 16 tiếng / 1 ngày, tức là từ 1 ca lên 2 ca sản xuất mà vẫn đảm bảo được sự ổn định và tin cậy làm việc của thiết bị, cũng như đảm bảo về chất lượng của sản phẩm. Chỉ có đến khi đó, bài toán về hiệu quả chi phí đầu tư của thiết bị mới thực sự bắt đầu có giá trị khi thông số về “mức độ sẵn sàng” của thiết bị được nâng lên từ 33% thành 66%, tương ứng lần lượt với 1 ca và 2 ca sản xuất. Do đó, càng phải siết chặt công tác đảm bảo sự hoạt động ổn định của thiết bị thông qua các hoạt động bảo trì và quản lý thiết bị hơn nữa.
Tham khảo khóa học "Bảo trì bảo dưỡng thiết bị sản xuất" do các giảng viên chuyên nghiệp tại trường Đào tạo Quản lý Kỹ năng SAM giảng dạy.
---------------------------------------------------------------------------------------------------------------
Mọi thông tin chi tiết về khóa học, Anh/ Chị có thể liên hệ BP. Tư vấn Trường SAM qua
Số điện thoại: (08)35 178848 - 35 178849
Hoặc email: info@sam.edu.vn; tuvan@sam.edu.vn

Xem thông tin chi tiết Chương trình Tri ân khách hàng tại đây